What are HMI and SCADA systems and how are they used in industrial automation?
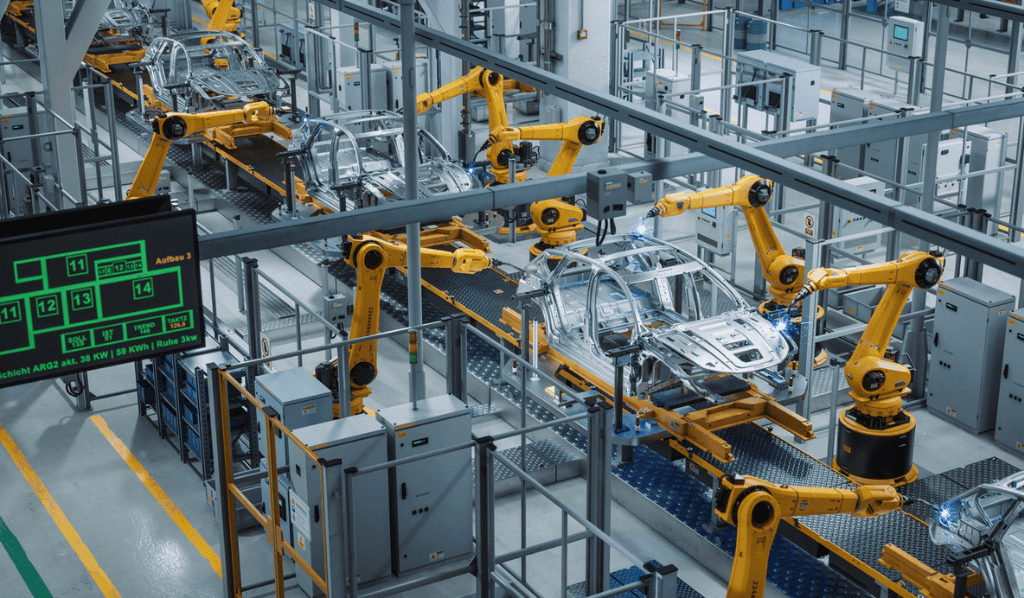
The SCADA industry is growing due to the significant demand for industrial mobility solutions and the increasing need for infrastructure and transportation development in smart cities. It is predicted that the SCADA market will grow from USD 9.8 billion in 2022 to USD 14.2 billion by 2027. Let’s dive deeper into industrial automation tech and get a basic understanding of what it’s all about.
What is a SCADA system?
SCADA stands for Supervisory Control and Data Acquisition. It’s a platform that consists of hardware and software: computers, sensors, networks, human-machine interfaces, and other components. SCADA systems are used for the supervision of industrial processes.
What is SCADA and why it is used? We can think of a SCADA system as a large-scale system for monitoring and controlling a complex process involving dozens or hundreds of equipment items. SCADA is a centralized control pane that collects data from all the sensors and transmits it to the software. The software then interprets the data and shows it comprehensively.
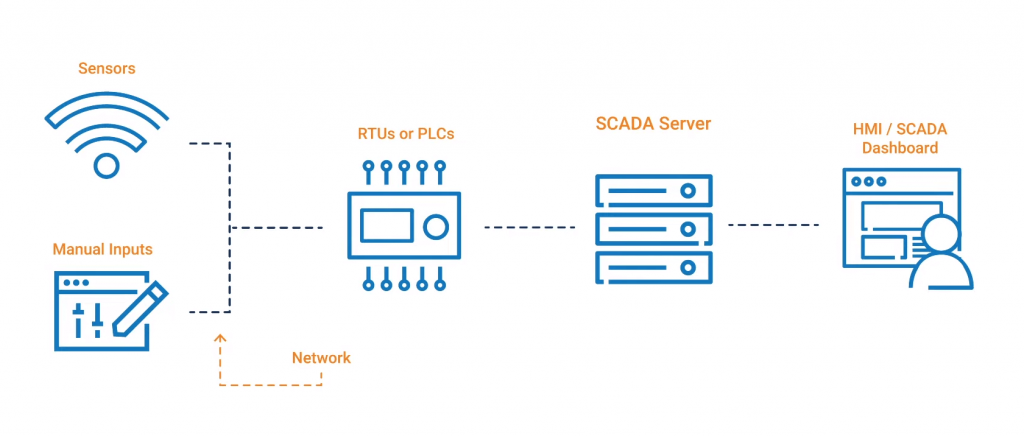
Where is SCADA used?
SCADA is a system consisting of many components and is mostly used in plants, factories, and other organizations using industrial automation. Industries that use SCADA systems include:
Oil and gas
Water systems
Food and beverage
Manufacturing
Transportation
Utilities
The potential of SCADA systems
In manufacturing environments, operators are responsible for overseeing numerous pieces of equipment. HMI and SCADA solutions enable personnel to precisely monitor, control, and visualize every aspect of their operations from a centralized location. SCADA in manufacturing industries provides operators with improved situational awareness, mobility of visualization, and better equipment control. By using new and high-performance HMI/SCADA software, operators can reduce the time spent navigating and quickly find critical data, boosting their productivity.
SCADA systems offer valuable insights into the operation of complex systems and can alert operators about potential issues before they escalate. Moreover, SCADA systems can facilitate the optimization of industrial processes, resulting in reduced energy consumption, increased output, and lower maintenance expenses.
SCADA is an automated control process widely used in large industries like manufacturing, construction, and engineering facilities for industrial automation. The use of SCADA in industrial automation allows for making data-driven decisions and providing greater control over industrial processes.
Core components of SCADA systems
SCADA connects equipment with controlling software and human operators. For proper work, SCADA requires some key components that collect, interpret, and show the collected data.
Sensors
These are hardware elements that measure various indices of the equipment or environment. They can be attached to pretty much anything in a plant or factory and their measurement capabilities can differ in complexity. Sensors can detect simple on or off signals, or more complex measurements like pressure, temperature, humidity, proximity, etc.
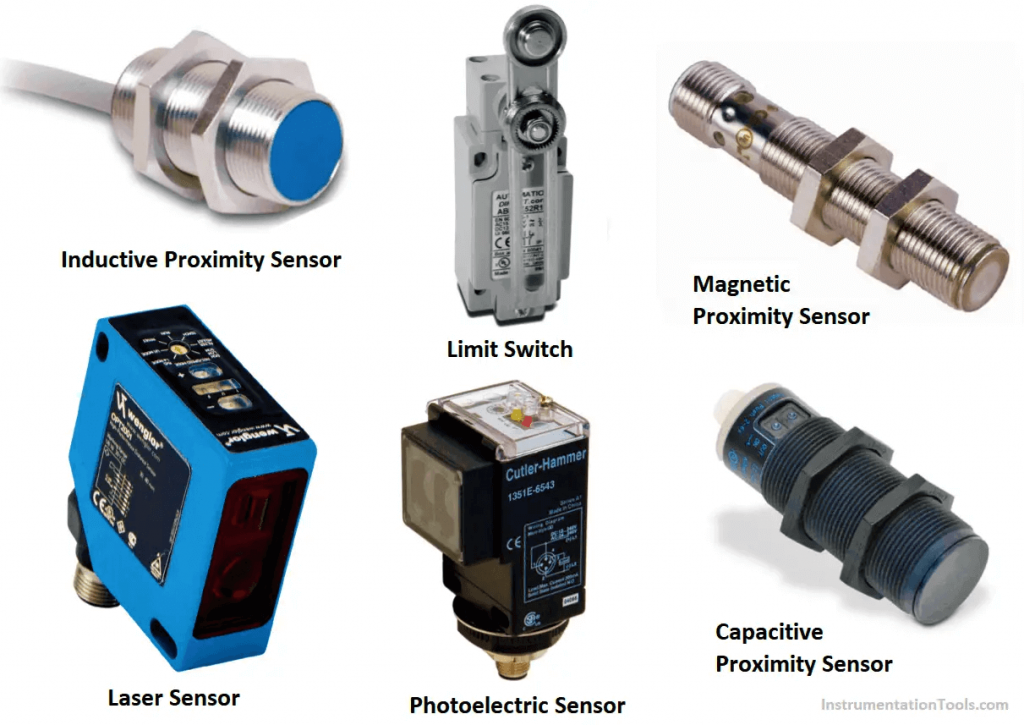
Data conversion units
The real-time data collected from sensors is only useful when it is comprehensive. To interpret the data, SCADA uses programmable logic controllers — PLCs and remote terminal units — RTUs.
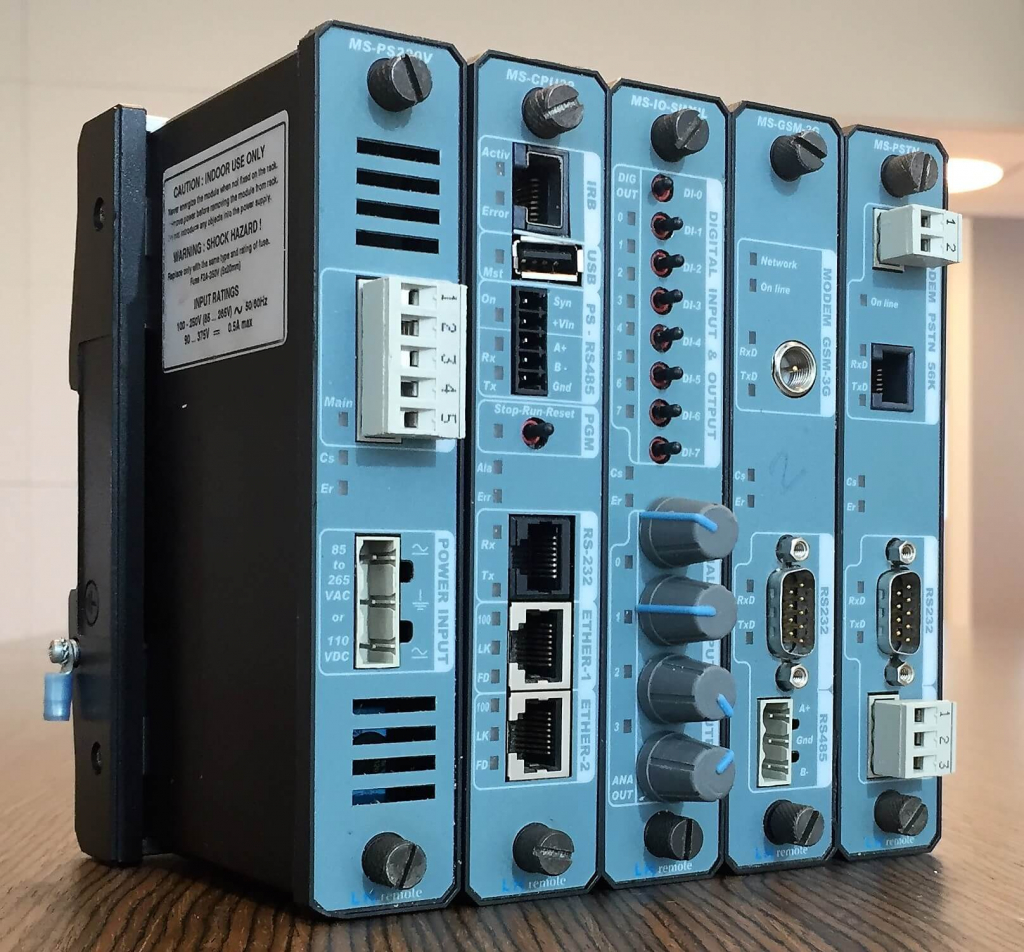
Human-machine interfaces
The converted data is sent to a human-machine interface — HMI. Maintenance teams find HMI SCADA software useful as it provides a complete picture of the entire process or system to a single operator. The data is presented in an easily understandable format, allowing employees to take control of specific equipment to make repairs or isolate failures. HMI is often confused with SCADA, but HMI and SCADA systems are different.
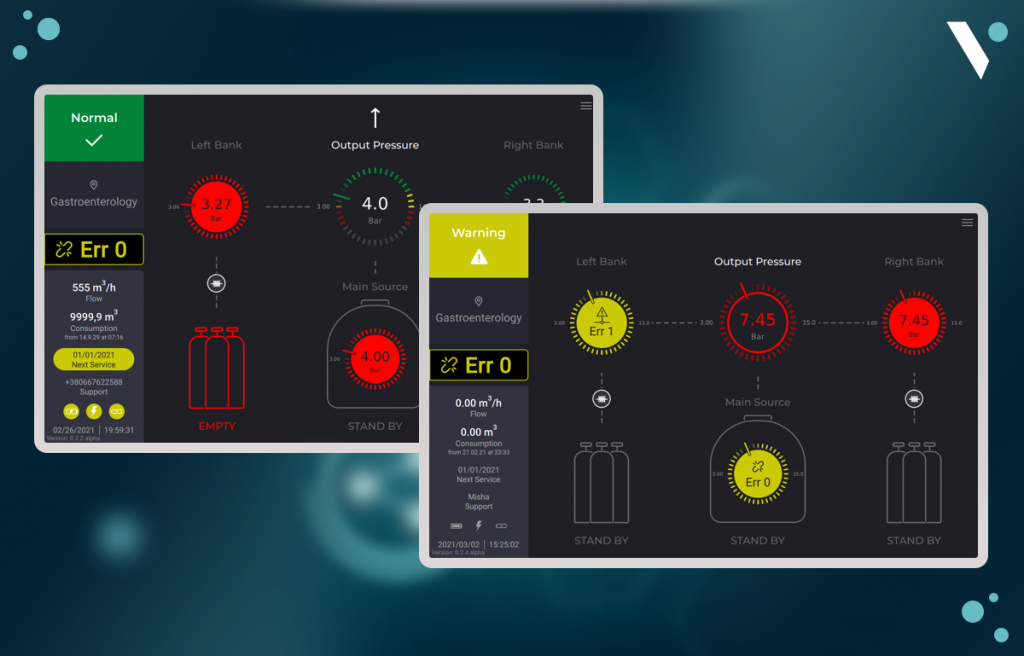
Network connections
The different components of SCADA are distributed across the plant, and they need some connectivity through a communication infrastructure network. Traditionally, telephone lines and circuits were employed to serve this purpose. However, new wireless alternatives are now available that utilize radio waves or cellular satellites.
Functions and benefits of SCADA systems
Basically, SCADA performs the following functions:
Remote access: operators can control the system without being present at the exact equipment item. This makes the monitoring process faster.
Data collection: sensors and actuators collect the data and transmit it to the HMI dashboard so the operator can make informed decisions.
Automation: the system can make automatic decisions based on the incoming data, which spares the need for human supervision for simple tasks.
Monitoring and alerting: SCADA monitors the completion of operations and processes, as well as deviations and failures. It sends alerts to the HMI when any human intervention is required.
Reporting: the system can generate various reports that help operators and supervisors track the performance of the equipment and make smarter decisions based on the actual data.
A well-designed SCADA system helps employees do their job at the facility. The benefits of SCADA system include:
Improved efficiency of the entire system
Smarter decisions based on the collected data
Increased safety for workers and equipment
Higher flexibility of the workflow due to remote monitoring
Reduced risks thanks to predictive mechanisms
What is an HMI system?
HMI is an abbreviation for human-machine interface. HMI functions as the primary interface between an operator and a machine or industrial control system. The interface consists of software and hardware allowing operators to interact with control devices, view process status, and access historical data.
Here’s basically how HMI works. The interface allows for keeping track of the equipment’s performance, giving commands, and changing settings. HMI can be accessed from a dedicated screen, mobile device, or any PC connected to the control network via a web browser.
The range of HMI displays can vary from a traditional physical control panel with buttons and indicator lights to an industrial PC with a color graphics display that runs specialized HMI software. Nowadays, touchscreen monitors, tablets for portable access to information, and wearable devices represent a significant portion of the HMI display market.
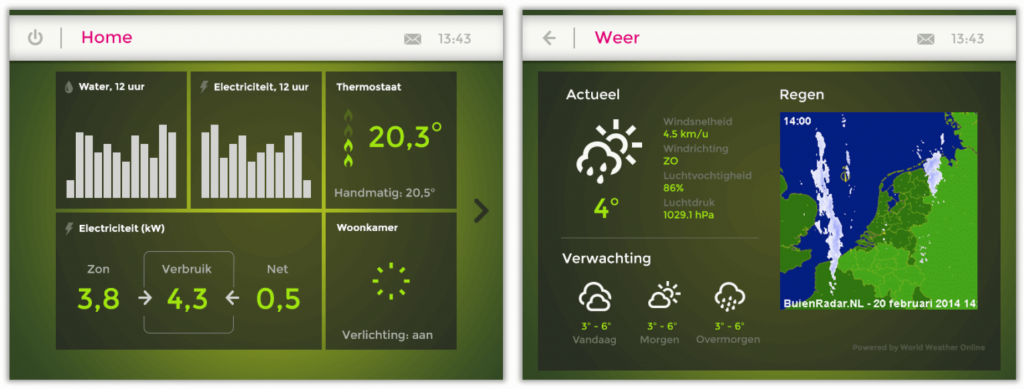
Key features and components of HMI systems
Graphical representations of the control process and digital controls replace manually activated switches, dials, and other controls. The use of HMI in industry allows operators to easily start and stop cycles, adjust set points, and perform other functions. Let’s break down the key HMI components and their features.
Hardware
It can be divided into input/output devices and processing units.
Input devices like touchscreens, keyboards, and buttons are used to provide commands;
Output devices like monitors, displays, and speakers reflect the current status of the equipment;
Processing units like an embedded computer or a standalone PC process user inputs and manage communication with the machines or system.
Software
Software is the heart of HMI. Software defines the UI, manages data communication, and executes commands. The application enables data logging, reporting, and analysis. Custom interfaces can include graphic elements like virtual buttons, sliders, charts, diagrams, animations, and more to make the interaction handy and comfortable.
Communication
HMI systems rely on communication to exchange information between the operator and the machine or system. Standard protocols like Modbus, Profibus, Ethernet/IP, and OPC ensure reliable data transmission for real-time monitoring and control. Wi-Fi and Bluetooth are also popular options that provide additional flexibility and mobility.
Use cases of HMI systems in industrial automation
Let’s mention some practical examples of what HMI can do for various industries.
Manufacturing: visualization and control of production lines, robotics, and computer numerical control machines.
Wastewater treatment: visualization and control of filtration, dosage of chemicals, and water routing flows.
Oil and gas industry: visualization of the pipeline status, pressure and fluid levels, and valves.
Energy management: visualization of generation and transmission of power, grid distribution.
Smart buildings: control of lighting, HVAC systems, video surveillance, and visualization of the building usage statistics.
HMI and SCADA: what they do, and how they work together
What is the difference between HMI and SCADA? In most cases, HMIs are situated near the equipment or process they control, allowing users to interact directly with them. A SCADA system is typically centralized in a control room, enabling remote monitoring of equipment and industrial processes. The difference between HMI and SCADA can be explained in the following way: HMI can be a part of SCADA, but SCADA cannot be a part of HMI.
SCADA and HMI in industrial automation gather data from various control devices like RTUs, PLCs, flow meters, and temperature controllers. This data is then displayed to the operator through a Human Machine Interface. The HMI provides real-time information to the operator, including custom-designed displays, alarms, trends, etc. Operators can use this information to make informed decisions and adjust machine settings accordingly.
HMI plays a crucial role in providing essential information to the human operator. The PLC system can detect any issues within the SCADA system, and the HMI can present the problem to the employee for immediate resolution.
HMI and SCADA in action
How HMI and SCADA systems complement each other
SCADA acts as a central database that stores and manages operations on a large scale. It works in tandem with the PLC, which facilitates communication and operation within the system. HMI is an interface that allows a human operator to interact with the whole SCADA system using screens, buttons, levers, or keyboards.
The role of HMI as the user-friendly front-end for interacting with the SCADA system
Human-machine interface is used to enhance productivity, reduce costs, improve reliability, and create safer working conditions. Within the facility, the user, hardware, and software must interact seamlessly to minimize errors, reduce stress for employees, and ensure confidence in the technologies utilized.
Trust is a key factor, as workers who lack confidence in the HMI may resort to working around it, leading to productivity loss, violation of company protocols, or even safety issues. Therefore, developers of embedded systems and industrial clients must prioritize good design that prioritizes the user’s needs.
Leveraging HMI and SCADA for industrial automation
If you’re planning to introduce a SCADA system into your facility, pay attention to the following questions:
What do I want to monitor?
What data do I need to collect?
How the data is going to be collected?
When you have a notion of how to use SCADA for your facility, you can add hardware and software to connect the system.
Our expertise in HMI / SCADA development
One of the technologies we use for HMI SCADA development is Qt, as it is flexible enough to build high-performance user-friendly graphical user interfaces. For instance, we built a GUI for a system that has to monitor and control gas supply and ratio in the hospital gas pipeline. Our engineers developed a nice animated HMI that would show the data changes in real time. Human operators can interact with the system using the tablet.
Besides HMIs, our engineers also develop IoT solutions, firmware, and embedded software that can serve industrial automation purposes. We work with sensors, real-time operating systems used in PLCs, data transmission protocols, network connectivity, and custom hardware and software.
Conclusion
SCADA and HMI are powerful tools that enhance the industrial automation process. SCADA is a wider term, meaning the entire supervisory system and HMI is a component that human operators use to interact with the system. HMI and SCADA complement each other to make the industrial automation process more efficient.